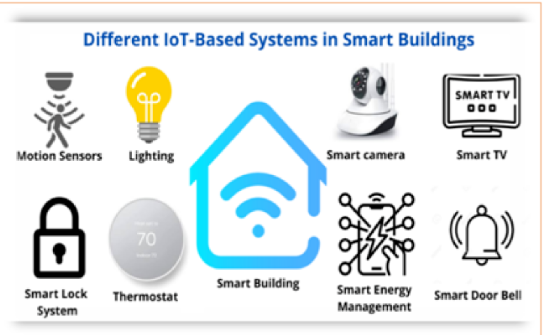
The artificial intelligence in IoT market is projected to surpass $153 billion by 2033, with smart manufacturing alone expected to reach $241 billion by 2028. These staggering numbers reflect the transformative potential of AI-IoT integration in industrial settings.We’ve observed how artificial intelligence and machine learning in IoT systems significantly enhance operational efficiency across industries. For instance, AI-driven automation reduces human error and operational costs, while predictive maintenance capabilities help prevent costly breakdowns. In smart manufacturing environments, interconnected devices communicate with centralized systems to optimize production processes and ensure consistent quality control. In this comprehensive guide, we’ll explore the practical aspects of implementing AI-powered IoT systems in industrial networks. We’ll cover everything from cost-benefit analysis and implementation strategies to real-world success stories and common challenges. By the end, you’ll have a clear roadmap for building smart industrial networks that deliver measurable results.
Cost-Benefit Analysis Framework
Building smart industrial networks requires careful financial analysis to justify the investment. Initially, organizations must evaluate both tangible and intangible benefits against implementation costs.
Initial Infrastructure Investment
The foundation of AI-IoT systems demands substantial hardware investments, including sensors, actuators, integrated circuits, and communication devices . Edge devices and specialized AI servers form another significant cost component, particularly for large scale deployments. Software costs encompass AI algorithm development, IoT management platforms, and integration expenses . Security infrastructure represents another crucial investment area. Organizations must allocate resources for robust cybersecurity measures, including secure communication protocols and continuous monitoring systems . Additionally, testing costs can be substantial, as AI-IoT systems require thorough validation before full deployment.
Operational Cost Reduction Metrics
Recent studies indicate that AI-IoT implementation yields substantial operational savings. According to industry research, 48.1% of organizations report that artificial intelligence and machine learning in IoT are essential for extracting valuable operational insights . Furthermore, 31.8% consider these technologies critical for data-driven operational decisions . The impact on cost reduction varies across business functions: Manufacturing departments report 10-19% cost reductions in 32% of cases Supply chain operations show 10-19% cost savings in 41% of implementations Marketing and sales teams achieve 10-19% cost reductions in 20% of cases
ROI Calculation Methods
ROI assessment for AI-IoT systems requires consideration of both hard and soft returns . Hard ROI focuses on quantifiable monetary gains, whereas soft ROI encompasses less tangible benefits such as improved employee satisfaction and enhanced skill acquisition.
To calculate ROI effectively, organizations should:
1. Define clear goals and key performance indicators
2. Establish baseline measurements
3. Track both implementation and ongoing maintenance costs
4. Monitor performance metrics continuously
The basic ROI formula divides net benefits by total expenses and multiplies by 100 . Nevertheless, this calculation should account for various factors including:
Upfront and recurring costs
Training expenses
Maintenance requirements
Data quality management
Moreover, organizations must consider the cost of delayed implementation. A recent report estimates the global smart factory migration challenge exceeds $400 billion over the next five years, with Europe alone accounting for $137.40 billion .
Implementation Strategy
Successful implementation of artificial intelligence and machine learning in IoT starts with careful planning and a focused approach. Organizations must align their technical capabilities with business objectives to avoid integration pitfalls and technical debt.
Pilot Project Selection
Selecting the right pilot project sets the foundation for long-term success. Primarily, organizations should aim for modest outcomes and focus on worker augmentation rather than replacement . A focused pilot allows teams to experiment, build prototypes, and expand as they develop IoT expertise . Five distinct approaches exist for initiating an IoT pilot project:
Internal part-time team (10-20% weekly commitment)
Dedicated full-time resources
Specialized IoT lab structure
Vendor IoT lab partnership
Independent IoT lab collaboration
Organizations without time constraints often choose the internal part-time model, specifically when gathering data to justify larger IoT initiatives. Consequently, companies with specific applications and committed timelines opt for dedicated full-time resources.
Team Structure and Roles
The complexity of AI-IoT projects demands diverse technical skills and collaborative expertise. Through 2023, approximately 50% of IT leaders will face challenges moving their AI projects beyond proof of concept to production . To overcome this hurdle, organizations must establish the right team structure.
Three primary organizational models have emerged:
1. Star Structure: Ideal for smaller companies starting their AI journey, featuring a centralized AI team serving all departments
2. Matrix Structure: Suited for larger organizations with multiple AI initiatives across product lines
3. Embedded Structure: Best for mature companies where AI is core to their products
Essential team roles include:
AI Architects: Focus on transformational architecture
Machine Learning Engineers: Handle production deployment
Data Scientists: Extract insights from complex data
Systems Integration Engineers: Manage existing software integration
Hardware Specialists: Design embedded systems
Ultimately, the ML engineer role shows the fastest growth in the AI/ML space, with projections indicating one ML engineer forevery 5-10 data scientists by 2023 . These specialists ensure AI platforms meet technical and business service level agreements while maintaining seamless collaboration with data scientists .
Real-world Success Stories
Leading organizations across industries demonstrate the practical value of artificial intelligence and machine learning in IoTthrough measurable outcomes and operational improvements.
Manufacturing Plant Case Study
Audi’s Edge Cloud for Production platform showcases the power of software-defined networking in manufacturing. The company’s implementation of industrial IoT solutions enables virtualized production assets and deterministic network control [2]. Notably, E80 Group enhanced their automated guided vehicles through AI-assisted monitoring, achieving real-time operations data collection and improved security .
Chemical Processing Facility Implementation Chemical manufacturers primarily utilize IoT sensors for precise process control and quality monitoring. Real-time data from these sensors measure critical parameters like temperature, pressure, and pH levels . Subsequently, cloud-based systems analyze this information to predict equipment failures and optimize maintenance schedules, resulting in a 30% reduction in maintenance costs.
Automotive Factory Deployment
Ford’s Cologne facility exemplifies advanced AI-IoT integration in automotive manufacturing. The plant implemented an AI-driven system for autonomous vehicle movement between assembly checkpoints . Indeed, this implementation includes vehicle-to infrastructure communication and sensor-based hazard detection, contributing to Ford’s goal of producing 600,000 electricvehicles annually in Europe by 2026 .
The automotive sector reports significant operational improvements through AI-IoT adoption:
42% of manufacturing workers cite training influence on company loyalty
75% of manufacturers achieved notable cost reductions after smart solution adoption
Production line efficiency increased by 15% through real-time monitoring
Energy Plant Integration
Energy companies demonstrate substantial gains through AI-IoT implementation. EDF Energy expanded its predictive maintenance capabilities by installing sensors in major asset components . Hence, the company now conducts advanced assessments of rotating equipment used in hydroelectric and nuclear production . Ørsted, a leader in offshore wind power, partnered with Vodafone and Microsoft to enable 4G data service and cloud-based analytics across its 1,300 offshore wind turbines . This integration facilitates real-time monitoring and predictive maintenance, optimizing operational efficiency and reducing unplanned repairs .
Common Implementation Challenges
Physical barriers and electromagnetic interference pose significant hurdles in implementing artificial intelligence and machine learning in IoT systems. These challenges demand careful consideration and strategic solutions.
Legacy System Integration Issues
Technical incompatibility emerges as a primary obstacle during integration. Organizations face difficulties when connecting older equipment with modern AI-IoT infrastructure, primarily due to the absence of standardized protocols for data processing between various devices and machines . The complexity of these systems creates visibility challenges for IT administrators and operational technology engineers. Without standardized methods for ensuring interoperability, securing systems that were never designed to be ‘smart’ becomes increasingly difficult . To address these integration challenges, organizations implement structured, incremental approaches to modernization. This strategy allows businesses to reduce technical debt gradually while enabling a more responsive IT environment . Through middleware and APIs, companies bridge the gap between legacy systems and AI components, minimizing the need for complete infrastructure overhaul .
Network Bandwidth Constraints
Bandwidth limitations present substantial obstacles in AI-IoT deployments. The requirements vary significantly across industrial applications:
Manufacturing environments demand high-speed connectivity for real-time operations
Industrial control systems require minimal bandwidth but ultra-low latency
Edge computing applications need substantial local processing capacity
During implementation, organizations encounter bandwidth-related challenges that affect system performance. The operational bandwidth of base stations typically operates at 20 MHz, allowing for approximately 100 Physical Resource Blocks . However, security features can add significant overhead, with Transport Layer Security (TLS) and Internet Protocol Security (IPsec) consuming more than 50% of available bandwidth .
Continuous data gathering for AI operations necessitates substantial network resources. The communication costs stem from multiple factors, including the number of communication rounds required for learning algorithms, channels used per round, and spectrum allocation per channel . Edge computing has emerged as a viable solution, allowing data processing closer to devices. Still, the limited capacity of IoT devices often forces ML processing to edge nodes or cloud systems .Outages introduce additional risk factors beyond typical connectivity issues. In industrial settings, sensor failures monitoring hazardous conditions like gas leaks could lead to critical situations. Smart grid disruptions might affect entire communities . Organizations must carefully evaluate connectivity requirements, considering factors like range, multiple location connectivity, and power consumption to minimize downtime risks .
Future-proofing Guidelines
Smart industrial networks demand strategic planning to accommodate future growth and technological advancements. Manufacturing facilities implementing artificial intelligence and machine learning in IoT systems must establish robust frameworks for long-term success.
Scalability Planning
Edge computing emerges as a cornerstone for scalable AI-IoT deployments. Organizations processing data closer to the source reduce latency by up to 90% while improving energy efficiency by 40% . Primarily, manufacturers optimize their value chain’s production through effective adoption of modern technologies . Network architecture requires modular design principles to support expansion. Cloud-based solutions paired with modular control platforms allow acceptance of technology advancements with minimal infrastructure changes . Essentially, plant owners prefer modularity to add equipment and infrastructure without disrupting existing production .
Technology Update Roadmap
Sustainability stands at the forefront of technology planning. Smart manufacturing enables services at lower prices through effective energy usage and reduced wastage . Organizations simultaneously track multiple parameters:
Energy consumption optimization
Resource utilization metrics
Process gap identification
Environmental impact assessment The roadmap must account for data growth patterns. Manufacturing facilities generate exponential amounts of monitoring data, making network capacity a key consideration . Soon, standardized parts across manufacturers will enable component sharing and manufacturing flexibility across locations .
Vendor Selection Criteria
Selecting the right vendor requires thorough evaluation of multiple capabilities. A structured assessment framework examines:
1. Technical Expertise: Evaluate past projects, client testimonials, and industry-specific case studies
2. Technology Stack: Assess programming frameworks, data management capabilities, and integration flexibility
3. Deployment Process: Review maintenance schedules, update protocols, and response times for technical issues
4. Scalability Track Record: Examine largest customer installations and complexity management capabilities he vendor’s agility in handling growing business needs proves critical . Organizations must verify the platform’s ability to operate seamlessly with existing tools and facilitate integration with third-party services . Straightaway, this assessment ensures alignment between vendor capabilities and business objectives. Pricing models require careful consideration, including implementation costs and ongoing maintenance charges . Service-level agreements, termination clauses, and intellectual property rights demand thorough legal review . Overall, the selection process must prioritize vendors offering comprehensive support throughout the solution lifecycle.
Conclusion
AI-powered IoT systems stand as transformative tools for modern industrial networks, offering substantial benefits when implemented strategically. Through careful cost-benefit analysis, organizations can expect operational cost reductions ranging from 10-19% across manufacturing, supply chain, and marketing functions. Success stories from industry leaders like Audi, Ford, and EDF Energy demonstrate the practical value of these systems. Their achievements highlight how structured implementation approaches, combined with the right team composition, lead to measurable improvements in efficiency and productivity. Smart industrial networks face significant challenges, particularly regarding legacy system integration and bandwidth constraints. However, organizations that follow systematic future-proofing guidelines achieve sustainable growth. Edge computing solutions reduce latency by 90% while improving energy efficiency by 40%, proving essential for scalable AI-IoT deployments.
Manufacturing facilities embracing these technologies position themselves advantageously in an increasingly competitive market. Their success depends on careful vendor selection, strategic scalability planning, and continuous technological adaptation. This comprehensive approach ensures long-term viability and positions organizations to capitalize on emerging opportunities in smart manufacturing.